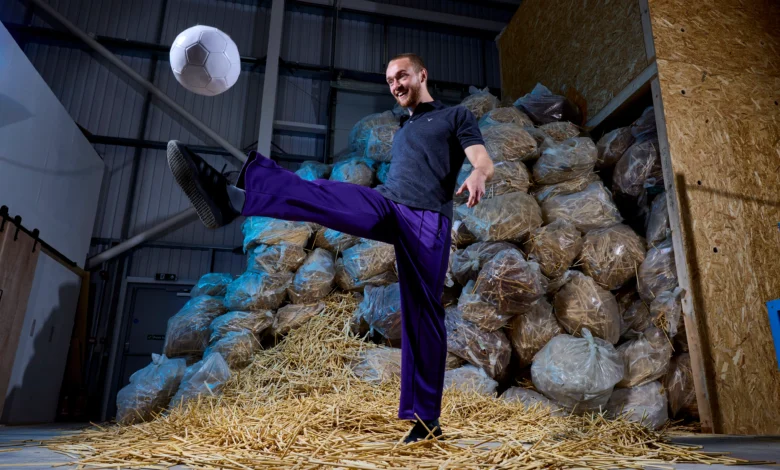
Footballer Tom Davies Launches Green Business, ChopValue, Transforming Chopsticks Into Statement Furniture
Chopsticks are recycled to create statement pieces of interior furniture at a new business which opens this week (14 June) led by footballer Tom Davies.
An estimated 80 billion chopsticks are used across the globe every year and without ChopValue UK’s efforts, are at risk of going straight to landfill.
ChopValue has proudly diverted over 160 million chopsticks from landfill while storing 7,890,770kg of CO2 emissions.
Opening in Liverpool, ChopValue UK is poised to contribute significantly to the growing impact and has already collected close to five million chopsticks ahead of its grand opening.
ChopValue UK is also setting a precedent as the first Microfactory location in the network to operate an electric van for community collections
Dramatic AI images have generated the scale of chopstick waste with images showing what 80 billion chopsticks would look like at UK Landmark, Big Ben.
With growing consumer adoption of sustainable products, the business is officially opening during Great Big Green Week (8-16 June), as the nation celebrates action on climate change with staff in its flagship Liverpool Microfactory.
In the next year, ChopValue UK is projected to convert 25 million chopsticks into premium climate positive products, saving up to 1,200 tonnes of CO2 emissions from being released into the atmosphere.
The company’s vision is to redefine the term ‘waste’ to ‘resource’, inspiring other businesses to join the circular economy, which is estimated to yield as much as £3.5 trillion in economic benefits over the next decade.*
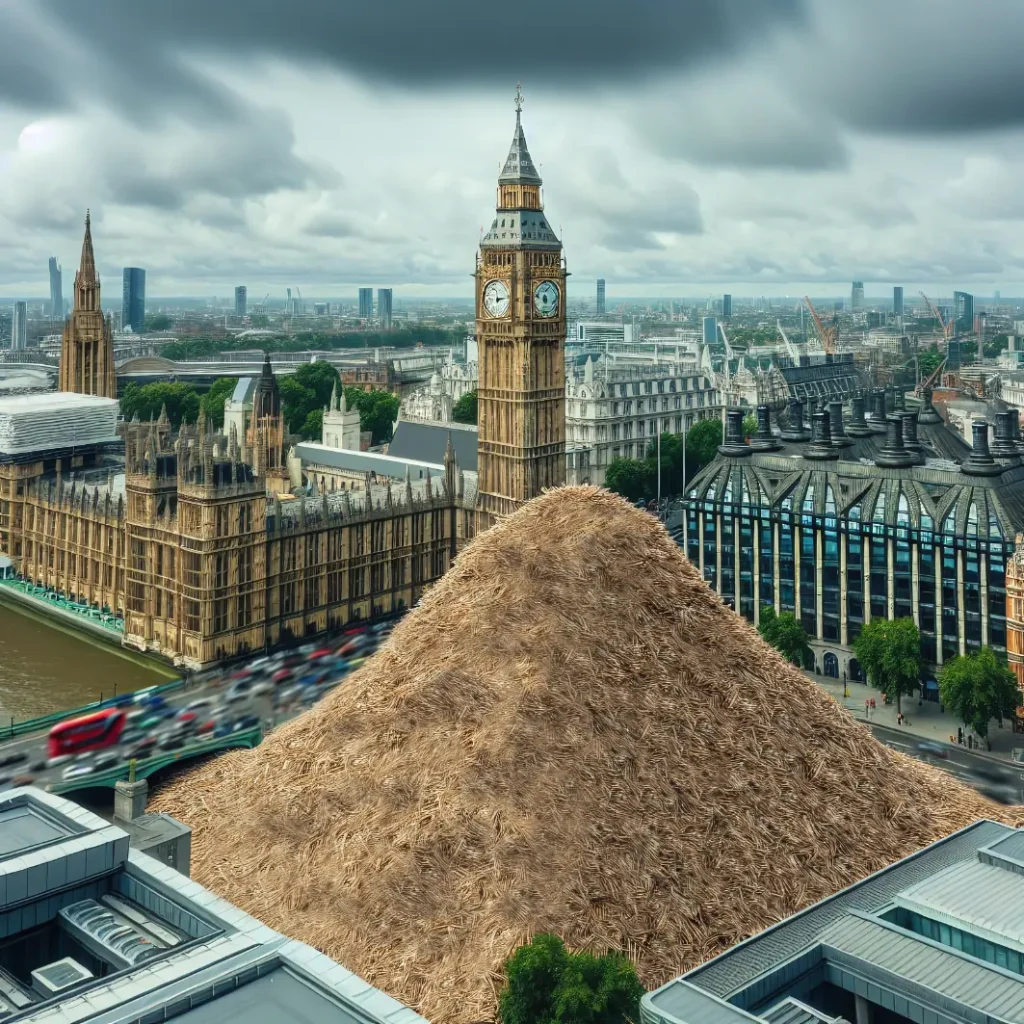
“We are paving the way for a greener future, where not only waste streams are transformed into valuable products made to last, but we can also source, produce, and distribute locally in our communities,” shared Tom Davies, Managing Director of ChopValue UK.
“I visit the Microfactory and experience the craft behind our products. I’ve enjoyed getting stuck into every aspect of the business, from literally sorting bags of used chopsticks after collection, to working the laser engraving machine.”
Davies also envisions providing a tangible route to sustainability for the sports brands he has cultivated strategic relationships with.
“As a footballer, I am grateful for the platform my career has provided me and am committed to lead by example. Educating others on subjects like the importance of sustainability and responsible manufacturing is my priority, with the goal of ensuring upcoming generations have the same resources we have been fortunate to have.”
“It’s our mission to leave no chopstick behind and given the extraordinary amount that are sent to landfill every year, there’s a huge job to be done,” shared Neil Sang, UK Director of ChopValue UK.
“ChopValue UK not only looks to turn waste into resource, but instil the importance of circularity and sustainability into the communities our Microfactory operates in. To launch in Liverpool has been a dream and we’ve relished training up our new employees, showing them a new set of green carpentry skills. The magic we are making in the Microfactory is special.”
“We work with local and national businesses alike and are already completing orders for a whole host of products; from restaurant tables to signage and desks for offices.”
ONCE A CHOPSTICK, NOW A STATEMENT: THE PROCESS
- Chopstick Collection: chopsticks are collected from partners such as restaurants, cafeterias, and shopping centres across the UK
- Chopstick Sorting: an electric sorting table sorts chopsticks, removing any waste and aligning all chopsticks into single orientation
- Resination: chopsticks are dipped into a water-based resin, an environmentally friendly alternative to the current resins used in the industry, allowing us to manufacture VOC-free products
- Drying: chopsticks are placed in an oven to reach the target moisture level and sanitised through immense heat
- Densification: chopsticks are densified in a heated hydraulic press that compresses the chopsticks into our engineered composite material, further sterilizing using high heat and pressure
- Product Manufacturing: high quality dense tiles are sanded and then built into desired products (e.g. restaurant tables, office desks, wall panelling)
- Finishing: we use a vegetable-based oil to enhance the natural colour and preserve the products for residential uses, or with a commercial finish for B2B projects
To find out more visit chopvalue.com
* World Economic Forum (2021) – This circular economy start-up turns millions of chopsticks into sustainable furniture. Available online at weforum.org/agenda/2021/01/recycle-chopsticks-furniture-circular-economy (2021).